Hydrogen testing facility expands to beat competition
One of the contenders for alternative shipping fuels is undergoing trials in Shoreham-by-Sea as the race for zero emission shipping steps up.
As the shipping industry battles to decarbonise, there’s a scrabble to test, iterate and scale a raft of technologies suited for different vessels and operational settings. Hydrogen is one challenger for the new fuel future, but questions remain from a technical, commercial and safety perspective. To help find answers, the UK environmental and engineering consultancy Ricardo has expanded its £2.5 million hydrogen facility so it can test large-scale marine engines.
In all, over the last three years, the company has invested over £3 million to build its capabilities for zero emission testing. These include testing on engines from small outboards right through to megawatt gensets and fuel cell systems.
“A key USP is our capability to design, manufacture and test single cylinder engines that allow precise control over a wide range of parameters independently to study in detail the combustion characteristics of decarbonised fuels and validate our digital twin analysis models,” says Tim Bassett, Head of Test at Ricardo.
Fuel cells are a key area of research, with the company specialising in multi-stack systems to meet the needs of the automotive, marine and aerospace markets. This means developing test proficiencies that can push these new fuels to their limits in the kinds of extremes that might be encountered in hostile marine environments.
“We currently have four hydrogen capable test facilities all sized for propulsion units up to 500kW,” explains Bassett. “Each cell is electrified, allowing testing of fuel cell systems or hydrogen internal combustion engines (H2ICE) with hybrid components. One cell is dedicated to fuel cell systems and is a climatic enclosure capable of testing down to -40°C and up to 90°C with humidity control of the intake air allowing fuel cell systems to be tested to extremes that may be experienced in service. In development is a multi-megawatt test area able to test containerised fuel cell systems.”
Bassett says dedicated test facilities such as in Shoreham-by-Sea are important to allow controlled development and validation of engine and fuel cell systems. “These facilities allow precise control of conditions to provide repeatable test conditions [and] allow system operation to be optimised,” he states. “Long duration validation tests can be run 24/7 in a safe and controlled environment monitored by an advanced test control system. Testing of this type simply cannot be conducted with the same levels of control, efficiency and safety in the field or on [a] vessel.”
This kind of proving ground is essential for new fuels, such as hydrogen. After the initial hype stoked by some policymakers about a new hydrogen economy, it has become clear that hydrogen faces some barriers for now.
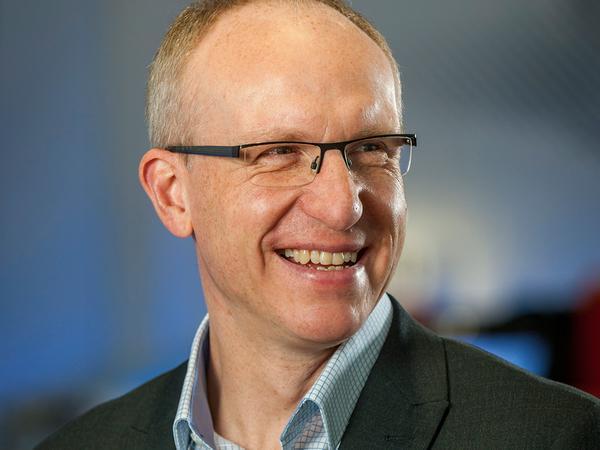
Still problems to overcome
“Hydrogen will not be a one size fits all solution,” acknowledges Adrian Greaney, Strategy, Technology & Innovation Director at Ricardo. “It will be one of several fuel solutions that form part of a decarbonised future for energy and transport. For all future fuels in maritime and other hard-to-abate sectors, what’s critical for greenhouse gas emissions is not just the fuel choice, but the feedstocks, energy sources and production pathways used to produce that fuel. In this respect, clean hydrogen production scale up is critical as a feedstock for e-methanol and e-ammonia, as well as being a low carbon fuel option in itself.”
According to the latest Clean Hydrogen Monitor report from Hydrogen Europe, industrial buyers have announced plans to consume 7.1 million tonnes of clean hydrogen annually by 2030 in a total of 268 projects across Europe. “This compares to just 0.11 million tonnes in 2023, so whilst there are many challenges in achieving final investment decisions for these projects, a significant [scaling] up of activity and clean hydrogen fuel availability is expected by 2030,” Greaney enthuses.
At present, the technology maturity is already well progressed but commercial maturity, including critical material supply, the supply chain and manufacturing, needs to advance to enable cost effective deployment at scale. “This alignment of investment in supply and demand solutions, with the necessary support during transition to bridge the gap between production costs and off takers’ willingness to pay, is a critical success factor to widespread adoption,” concludes Greaney.
For now, more mature fuels such as methanol have the commercial edge, as they already have established handling, bunkering, and storage infrastructure and can be more readily retrofitted into existing internal combustion engine-powered vessels. However, given methanol production pathways must transition from fossil fuel based to e-methanol or bio-methanol, it is anticipated that green (made using renewables) or blue (made using natural gas but with carbon capture and storage) hydrogen is likely to achieve a lower fuel cost by the mid-2030s.
Tell us what you think about this article by joining the discussion on IMarEST Connect.
Join IMarEST’s Ship Energy and Environment Special Interest Group to discover more about similar topics.
Main image: hydrogen gas molecules; credit: Shutterstock.
Inline image: Adrian Greaney, Strategy, Technology & Innovation Director, Ricardo; credit: Ricardo.